螺紋連接在接觸網(wǎng)零部件連接中使用廣泛,其具有結(jié)構(gòu)簡單、連接可靠、拆裝方便等優(yōu)點。由于列車通過時受電弓與接觸線垂向耦合引起系統(tǒng)振動,接觸網(wǎng)零部件在整個壽命周期內(nèi)需承受該振動約300萬次,此時,常規(guī)的螺紋連接裝置已不能滿足要求,對防松螺母的研制已勢在必行。
目前,行業(yè)內(nèi)較多地采用具有較好防松性能的錐壓抱緊螺母、偏心式防松螺母等,其結(jié)構(gòu)均為主副雙螺母型式。
普通的螺紋連接本身具有自鎖功能,螺紋緊固后,在連接副摩擦力的作用下,未施加附加扭矩時連接不會松動。
普通螺紋連接擰緊、松卸過程示意如圖 1 所示。
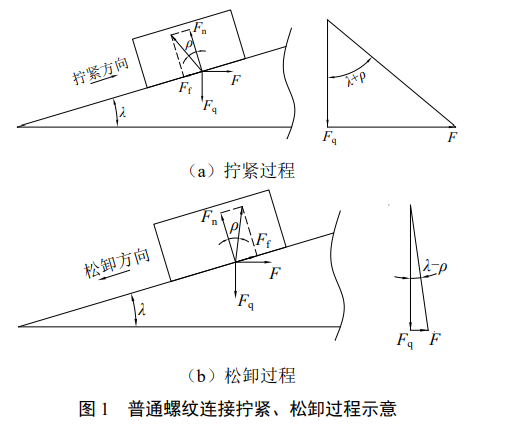
圖中F為水平推力,F(xiàn)q為軸向力,F(xiàn)f為摩擦力,F(xiàn)n為法向反力,λ為螺紋升角,ρ為當量摩擦角。螺紋擰緊時,滑塊沿著斜面上升,受到的滑動摩擦力沿斜面向下,根據(jù)力的多邊形平衡法則,得:

螺紋松卸時,滑塊沿斜面下降,受到的滑動摩擦力沿斜面向上,根據(jù)力的多邊形平衡法則,得:

普通牙型角為 60?,μ?為摩擦系數(shù),μ為當量摩擦系數(shù),則有:

則松退螺母所需要的力矩為:

式中:d 為直徑。
緊固件安裝連接后,螺紋承受了一定的初始預緊力。螺紋副表面的材料靠預緊力提供正壓力使螺紋之間的摩擦阻力最大。當外界環(huán)境出現(xiàn)變化,如振動、沖擊、交變載荷等情況,此時螺紋副靜載環(huán)境消失,螺紋副承受的預緊力可能突然衰減或瞬間消失,使螺紋副之間的摩擦力急劇下降;同時,由于被連接零件自身的慣性以及各零件之間的相互作用,帶動螺紋副朝松卸方向出現(xiàn)微小位移,長期出現(xiàn)該狀況時就會導致緊固件出現(xiàn)松脫現(xiàn)象。
普通連接型式螺紋之間本身存在間隙,當緊固件安裝后,實際只有2~3扣螺紋處于壓緊狀態(tài), 其余大部分螺紋處于虛接狀態(tài),這部分螺紋不能提供足夠的摩擦阻力來防止螺紋回退(圖 2)。
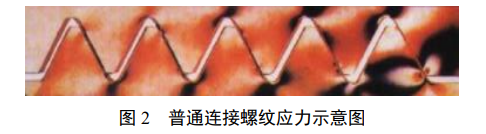
以 M12標準螺紋為例,M12-6g的螺栓配合M12-6H的螺母,查閱 GB/T 15756—2008《普通螺紋極限尺寸》,其最大螺紋間隙在徑向可達0.384 mm,而常規(guī)的螺紋安裝形式只能實現(xiàn)2~3扣螺紋接觸(軸向接觸)。這樣一來,徑向間隙和軸向間隙兩個因素累加,就會導致在現(xiàn)實環(huán)境中很多情況下會出現(xiàn)螺紋副松動的現(xiàn)象。
2 螺紋防松過程分析
觀察電氣化鐵路接觸網(wǎng)系統(tǒng)的防松緊固裝置中運用較多的錐壓抱緊螺母和偏心式防松螺母,其 防松效果相較于普通螺紋連接型式有了明顯的提升,可大體歸納為:(1)消除螺紋副的固有間隙, 或是將間隙進行定向;(2)增加螺紋副材料的接觸 面積或接觸點數(shù)量;(3)通過增加螺紋副材料之間的正壓力增加螺紋摩擦力。
以上3點歸納可視同為螺紋防松需要同時解決螺紋副固有的間隙問題、螺紋副材料的接觸面積 問題、螺紋副螺紋之間的摩擦力問題。在了解了影響螺紋緊固件松動的主要因素后,下文從影響因素的本質(zhì)入手逐一進行分析。
2.1 螺紋副固有的間隙問題
螺紋副的間隙是固有的,其生產(chǎn)加工機制決定了間隙的存在及不穩(wěn)定性,只能在使用過程中予以消除或改善。螺紋間隙可分為軸向間隙與徑向間隙。
對于軸向間隙,由于螺紋在軸向需要承受一定的預緊力,對該預緊力一般有一定的限制要求,單 方面通過施加扭矩雖然可消除更多的軸向間隙,但卻破壞了預緊力,失去了緊固件作為連接的意義,得不償失。
對于徑向間隙,螺母端面在安裝狀態(tài)下與螺紋軸向一般為垂直關系,平行于螺母端面施加一個徑向力并不會影響螺母承受的預緊力,當該徑向力克服了螺母端面與平墊圈之間的摩擦力時,螺母沿徑向移動,螺紋副的徑向間隙就會被定向(單邊消除)。
2.2 螺紋副材料的接觸面積問題
由上文可知,普通螺紋連接的實際情況是僅2~3扣螺紋處于接觸狀態(tài),其余螺紋處于虛接狀態(tài),這是由螺紋的連接機制導致。為了使螺母高度范圍內(nèi)更多的螺紋互相接觸,同時不破壞螺母的初始預緊力,這就要求螺母在軸向不能移動,故可以考慮螺母在徑向上接觸更多的螺紋。螺紋的徑向尺寸理論上是一致的,只要移動螺母,便可使螺紋副上更多的螺紋互相接觸。
2.3 螺紋副螺紋之間的摩擦力問題
當需要增大摩擦力時,螺紋副的材料須有一定的正壓力,正壓力越大摩擦力越大。外界能夠施加于螺母的力只有一個扭矩,如果該扭矩直接作用于螺紋,由于螺紋是圓周結(jié)構(gòu),徑向分力互相抵消, 螺紋上只剩軸向分力,為增大螺紋副上的壓力,只有增大扭矩,而增加扭矩會破壞螺母的初始預緊力,不可行。此時需要通過結(jié)構(gòu)設計,使螺母承受一定的徑向力,然后通過增加螺紋副上的壓力實現(xiàn)螺紋之間摩擦力的增大。
在進行單螺母防松結(jié)構(gòu)設計時,首先需要考慮不能破壞螺母是承擔預緊力的主要載體這個基本特點,同時還要考慮螺母扭矩不能出現(xiàn)大的變化, 在此基礎上再進行設計。
單螺母防松結(jié)構(gòu)設計需同時解決上述3個問題,應采取相應輔助措施使螺紋副之間的接觸產(chǎn)生有效變化。緊固件的連接通常需要在螺母與被連接基體之間安裝墊圈,在墊圈與螺母之間進行結(jié)構(gòu)設計,不會大幅增加產(chǎn)品高度,也不會顛覆產(chǎn)品的加 工工藝。
通過上述防松過程分析可知,單螺母防松首先需要解決的是如何給螺母本體施加一個徑向(水平)力,通過分析,該徑向力須來自第三方。普通平墊圈在受到螺母下行壓力時,墊圈隨著螺母下移,螺母和平墊圈均不會產(chǎn)生徑向位移(圖 3(a)),而當需要螺母在下行過程中同時產(chǎn)生徑向移動時,可在墊圈上設置輔助斜面(圖 3(b))。
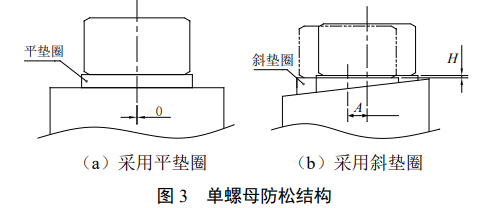
如圖3(b)所示,螺母下降相同高度,普通平面結(jié)構(gòu)的平墊圈水平位移為 0,而斜面結(jié)構(gòu)的斜墊圈產(chǎn)生了水平位移A。觀察發(fā)現(xiàn),斜墊圈產(chǎn)生的位移A并沒有對螺母產(chǎn)生徑向作用,螺母本身并未出現(xiàn)水平位移。
為使斜墊圈的徑向位移帶動螺母產(chǎn)生徑向壓力,可在墊圈上設置凸臺,螺母上設置凹槽,凸臺與凹槽相互配合,如圖4所示。
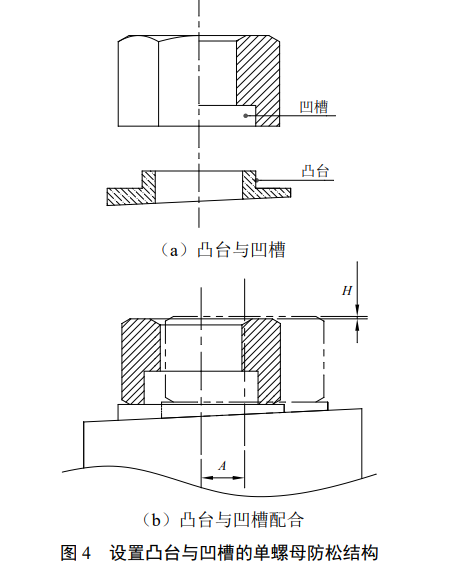
如此一來,螺母受到緊固力矩帶動斜墊圈下行, 下行過程中受斜面影響,斜墊圈會朝徑向一側(cè)移動,此時又由于凸臺與凹槽的相互配合,使螺母與斜墊圈形成一體,螺母也會向徑向一側(cè)移動。
在實際安裝過程中,一般情況下,被連接基體表面均為平面,采用斜墊圈時,螺母安裝時會發(fā)生偏扭,為此需增加一個轉(zhuǎn)換墊圈,使緊固裝置實現(xiàn)平面連接的防松,如圖5所示。
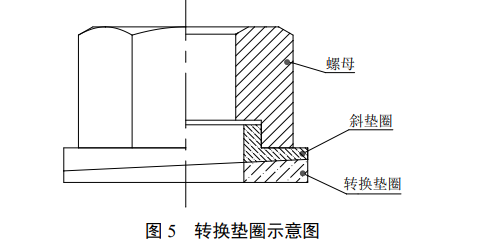
通過在單螺母下方增設斜墊圈,螺母與斜墊圈形成一體,螺母下行過程中受到斜墊圈徑向擠壓, 螺母產(chǎn)生一個徑向位移 A1,螺紋副之間的接觸點增多(圖 6)。經(jīng)驗證,要消除M12-6g/6H螺紋副之間0.384mm的固有螺紋間隙,可將斜墊圈斜度設置為6,此時螺母只需下行0.04mm即可;當螺母繼續(xù)下行時,螺紋副材料開始產(chǎn)生彈性變形, 摩擦力增加至最大狀態(tài)。
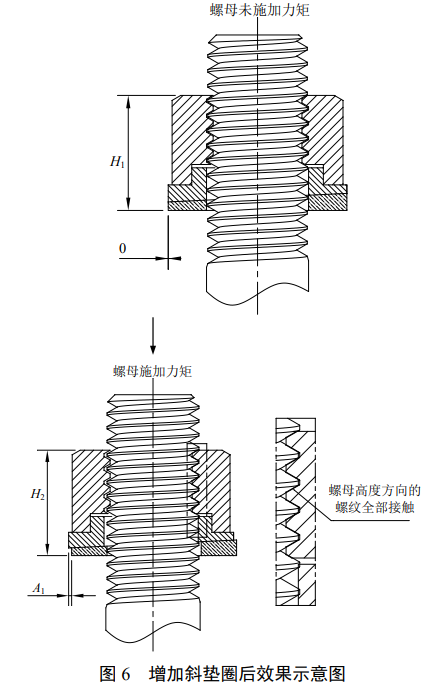
經(jīng)過上述設計,螺母本身依然作為預緊力載體, 預緊力變化不大但同時實現(xiàn)了消除單向定位螺紋間隙和增加螺紋副之間的觸點及接觸面積的目的, 并有效增加了螺紋副的徑向正壓力,使材料在徑向產(chǎn)生彈性變形,提高了材料之間的摩擦力。
當螺母擰緊后,螺母與螺栓之間的螺紋間隙消失,兩者形成抱緊關系,螺母與螺栓都處于防松狀態(tài),并且,在軸向預緊力和徑向正壓力的作用下, 螺紋副材料處于彈性接觸狀態(tài),此時摩擦力最大, 同時可以抵消一部分螺紋副振動。
螺紋受力如圖7所示,圖中,F(xiàn)1為螺紋副之間的摩擦力,F(xiàn)2為螺母與斜墊圈之間的摩擦力,L1為螺栓中徑,L2為凸臺外徑,M為螺母與斜墊圈之間摩擦力產(chǎn)生的力矩。螺母安裝后的力矩平衡式為F1×L1+M=F2×L2或F1×L1=F2×L2+M,為了不受力矩M影響,可在螺母與斜墊圈之間增加一些防滑齒(圖 8),使螺母與斜墊圈不產(chǎn)生滑動(形成一體),由此可得力矩平衡式:F1×L1= F2×L2。
由于L1永遠小于L2,故 F1>F2,即螺紋副之間摩擦力大于螺母與斜墊圈之間的摩擦力,滑動首先會發(fā)生在螺母和斜墊圈之間。當斜墊圈出現(xiàn)旋轉(zhuǎn)趨勢時,由于斜墊圈傾斜角度不小于6,而螺紋升角一般不大于3(圖 9),斜墊圈旋轉(zhuǎn)就會與轉(zhuǎn)換墊圈發(fā)生鎖死,因此斜墊圈不會松動,螺紋副也不會發(fā)生松動[3]。轉(zhuǎn)換墊圈出現(xiàn)旋轉(zhuǎn)趨勢時,同理。
以上設計目的均為消除螺紋間隙,增加螺紋副的摩擦力,使螺母與螺栓之間形成抱緊關系,實現(xiàn)螺母與螺栓同時防松。
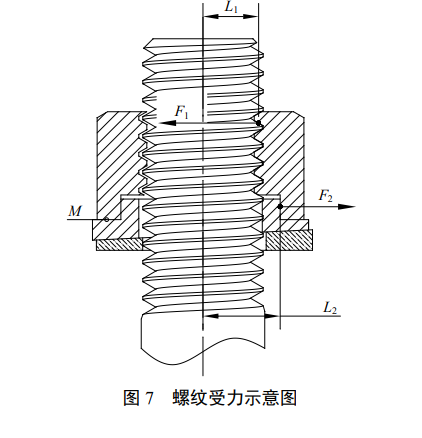
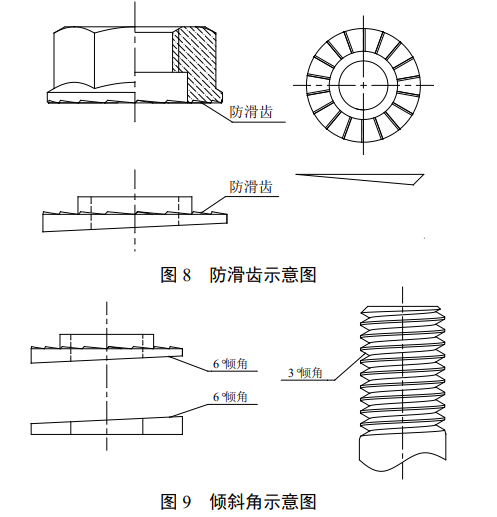
該設計的優(yōu)點:(1)螺母結(jié)構(gòu)簡單,可實現(xiàn)冷鐓批量生產(chǎn),不需單獨增加工序;(2)螺母與螺栓同時實現(xiàn)防松,且螺栓不需要特制,配置標準螺栓即可;(3)對被連接的基體無特殊要求,無需設置防轉(zhuǎn)槽等;;(4)單顆螺母配合斜墊圈實現(xiàn)防松,防松裝置整體尺寸較小,可適用于狹小空間或特殊位置的安裝。
本文提出單螺母防松結(jié)構(gòu)設計,借鑒現(xiàn)有成熟的防松產(chǎn)品,從理論上分析緊固件防松過程,總結(jié)影響因素并提出解決思路,使螺母防松裝置能夠?qū)崿F(xiàn)輕量化、簡單化,同時還能夠達到良好的防松效果,一定程度上解決了狹小空間或特殊位置處緊固件連接的松脫問題,為接觸網(wǎng)零部件防松提供了更多的選擇。